Sponge iron
خانه > Sponge iron
What is sponge iron?
According to the statement and the research that has been done, we can give you a general and comprehensive definition of sponge iron. Sponge iron was used for the first time around 2009 in induction furnaces in Iran, because of this, in the early years, despite its low and declining quality, there was no shortage of scrap.
Despite the fact that induction furnaces were purchased from China and India; But they also did not encourage Iran to do this. For the first time, one of the induction factories in Yazd used sponge iron. But again, it took a long time for other factories to accept it; Because the use of sponge iron, unlike other tools such as rebar, angle and heavy studs, had a negative result.
Most of the users and producers considered its negative impact due to the engineers’ lack of familiarity with recharging and believed that compared to scrap, its phosphorus and sulfur disturb the balance and analysis of melting, and thirdly, sponge iron requires high carbon. has
But today, we see with our own eyes that even small and medium-sized steel factories use sponge iron, and we can consider the reason for this to be Iran’s easy and direct access to natural resources.
Now that we know the history of sponge iron, it is better to go back to our question and explain once again what is sponge iron. Sponge iron is also called DRI direct reduction iron. Sponge iron, or direct reduction iron, is produced from the direct oxidation and reduction of iron ore in the form of agglomerate, clay, pellets, or pellets to iron by reduction gas or elemental carbon produced from natural gas or coal.
A clear example of that is heating iron ore in a furnace at a temperature above 800 to 1200 degrees Celsius, that is, 1470 to 2190 degrees Fahrenheit, in the presence of a regenerating synthesis gas, a combination of hydrogen and carbon monoxide. It is better to know that after recovery the metal becomes toxic.
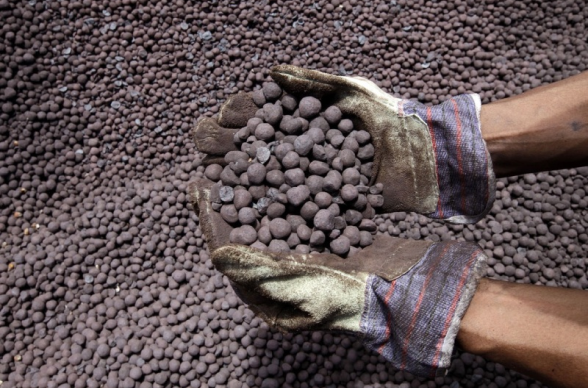
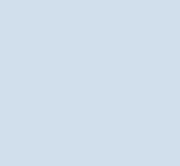
What is the use of sponge iron in industries?
What is sponge iron and describe its use in different industries! What factories produce sponge iron? There are many people who are familiar with the concepts and meanings of terms and words of the steel industry and its tools and know how each steel product is produced and what is the use of each one! Sponge iron, which some of you may be familiar with and others are hearing this term for the first time; It is obtained from the direct recovery of iron ore.
Many people, when they hear a word for the first time, like to research about the use of iron and also know about its advantages and disadvantages during this research. In the article and in the following content, we intend; Explain the concepts of sponge iron, rebar, angle and heavy studs in a complete and comprehensive way so that you know their use and role.
Application of sponge iron
In order to learn about the use of sponge iron; You should also know its general history, we mentioned its Iranian history in the previous article, but regarding its global history, we must state that the manufacturing and production of sponge iron was one of the first methods of obtaining iron in the Middle East and Europe; But in China, the construction of blast furnaces to obtain iron and cast iron goes back to 500 years BC. Now it’s time to know the application of sponge iron.
Sponge iron is not used by itself; In other words, it is not only beneficial for industries, but engineers and factories producing sponge iron know sponge iron as a suitable and affordable substitute for iron waste, that is, they can use a high percentage of raw materials to provide the melting needed by steelmaking units. use sponge iron instead of waste, so in short, we must say that the most important and first use of sponge iron is its use in induction furnaces, which can be used instead of scrap with a probability of 50%.
Sponge iron is also used in the iron and steel industry, because of its high iron content and special chemical compounds that produce strong and high-quality steel. And finally, sponge iron is used to make and produce all kinds of ingots in electric arc furnaces, which increases productivity and quality of ingots.
It goes without saying that sponge iron is used in the industry of weapons and iron tools for the reasons we mentioned before, but like any other tool, besides having many uses and countless benefits, it also has risks that we can refer to things such as the ability to oxidize, rust Let’s mention high burnability and flammability in the paste state.
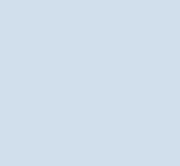
Advantages of sponge iron
Many iron producers these days prefer to make steel and steel alloys directly from sponge iron. Sponge iron has more advantages than scrap iron. But iron scrap in the reduction furnace during the oxidation operation and production of steel sheet creates more nitrogen and produces steel sheet with a lower grade percentage. Here are some of the most important advantages of sponge iron:
The percentage of iron purity in sponge iron reaches 95%. Therefore, it is much easier to use than scrap iron due to the lack of impurities.
Sponge iron is much more economical than other raw materials due to the low consumption of energy and water during melting.
When melted, it has a small amount of nitrogen in its content, and therefore the products produced from it will have better quality.
Sponge iron is easy to store and easy to move and carry.
The use of sponge iron in melting furnaces does not have the risk of explosion due to the presence of impurities.
During production, it uses little oxygen to be produced.
The most important advantages of using this type of porous pellet is not to damage the furnace wall.
The quality of the products cast with sponge iron is very high due to its consistency and lack of toxic elements.
Its metallurgical and melting operations are easily performed due to the lack of filtration, and accordingly, the performance of the furnaces will be performed well.
Disadvantages of sponge iron
In addition to having many advantages, sponge iron or porous pellets also have some disadvantages to use. Here are some of these disadvantages:
In order to enter the production cycle of steel sheets and alloys, sponge iron must go through many stages. But scrap iron does not have this problem.
Because there are many steps to transform sponge iron into steel, various products with various compounds are created during production.
Pellets created in different stages of steel production do not melt at the same temperature and this is a bit troublesome.
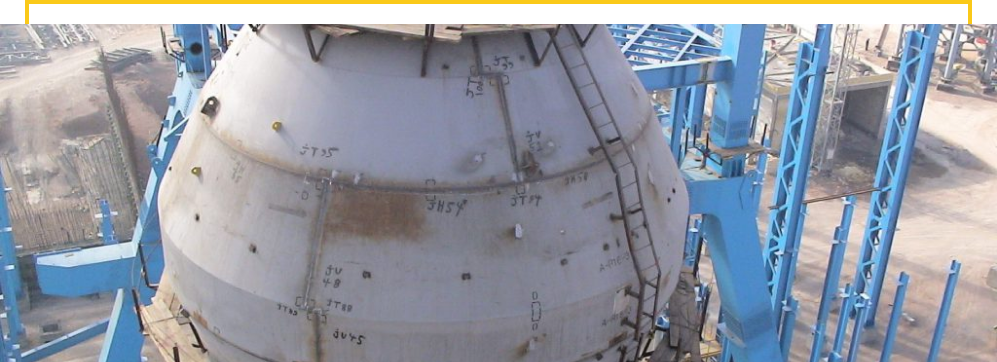
Sponge iron factory
We reached the important part of the article; Because no matter how familiar we are with the meaning and application of the tools and even the prices of the products in seconds and moments, if we cannot find a reliable factory to buy the product, all the actions we take are useless. In this part of the article, we would like to introduce a number of sponge iron production factories according to your requests, so that you can compare their quality and price before buying and make the best decision so that you don’t regret it later.
Foulad Mobarake sponge iron production factory: The first factory in the production of sponge iron is Foulad Mobarakeh; Because it is the largest and most reliable sponge iron factory in Iran. Mobarakeh Steel Factory now has a 20% share of the flat steel sheet market in the region, and the more important thing is that the production capacity of the factory is 4.11 million tons.
Gahar Sirjan Steel Factory: Kavian Gahar Sirjan Steel Factory manufactures and produces concentrates and pellets. Kavian Gohar Company has been able to improve the quality of its products by providing advanced equipment in the production lines of the factory.
Spat Asia Steel Factory: Another famous and reliable factory in Iran in the production of sponge iron is Spat Asia Steel Factory. Spud Steel Factory plays an important role and has a significant impact on the production of concentrate and pellets by buying and selling raw materials related to the steel industry.
Saina Steel Factory in Golpa: Saina Steel Factory has a 25-year history in the field of sponge iron production and plays an important and vital role in the mining industry of Iran, and is also one of the suppliers of ferroalloy and ingot production.
Rehnamon Sanat Steel Company: Rehnamon Sanat Steel Company, like Gohar Sirjan Steel Company, started its activity in the production of concentrates and pellets in recent years, in the first years it produced construction and industrial iron, but now it has a special department for iron production. It has a sponge.
Ardakan Steel Factory: This factory is not one of the factories that produces concentrates and pellets and is also active in the production of sponge iron. Of course, Ardakan Steel Factory supplies the domestic needs of many steel factories. In the production line of Ardakan steel factory, the concentrate of steel smelting and rolling is produced.
Parsian Superior Steel Factory: Superior Steel Factory is one of the most famous steel factories and its fame is due to being a supplier of raw materials for the steel industry.
Buy sponge iron
This article is not written and uploaded only for those interested in these concepts; Our goal is to inform and acquaint people with the uses and prices of sponge iron; It is possible that people reading the article are inquiring about buying sponge iron, so we are going to mention some points about buying sponge iron so that you know what actions you should take when buying sponge iron.
You can buy sponge iron from stores and iron factories, in the following, we will finish the article by introducing sponge iron factories in all parts and regions of the country, as well as mentioning the price of iron.
Buying sponge iron is one of the most controversial topics in the field of iron and steel and alloy sheets. Companies may mainly face problems to buy sponge iron. Steel and alloy production companies have to buy the sponge iron they need from other companies. The purchase of sponge iron is carried out at the daily price and in accordance with the global selling price.
Some companies and factories producing steel and hot steel sheets produce their own sponge iron. In fact, it is very cost-effective for steel and alloy sheet companies to buy iron ore and convert it into sponge iron in their induction furnaces, and then make steel alloys in the steel production department. But in many steel companies, this does not happen.
Currently, many sponge iron manufacturing companies sell this product through internet websites. In these sites, you can inquire about the price of buying and selling sponge iron directly, and then make a transaction.
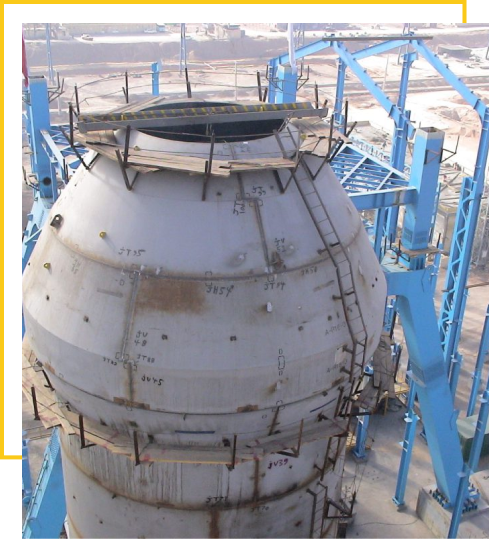
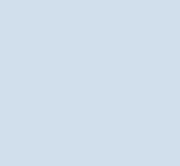
Sponge iron production process using gas and coal sources
To produce sponge iron in steel factories, iron ore in the furnace can be regenerated by two methods. These two methods include the following:
Regeneration method with Gas based gas reserves
Reclamation method with Coal based coal reserves
In different countries of steel production, each of these reserves can be used for induction, which is related to the amount of available and available reserves. In Iran, due to the large reserves of natural gas, gas is used to induce iron ore in Khuzestan steel and Mobarakeh steel factories.
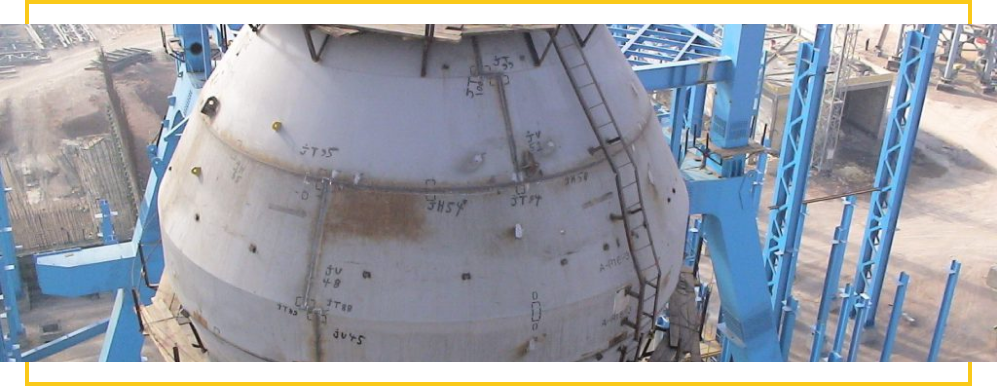
What is sponge iron briquette?
Sponge iron briquettes are composed of iron shards, coal dust or mixed materials such as sponge iron or iron soil and pleats. Sponge iron briquettes are similar to compressed sponge iron molds
Sponge iron briquettes are highly sought after due to their special shape and form, as well as their efficiency, easier storage, and simple transportation. As far as the briquetting industry in the country and the steel industry are developing.
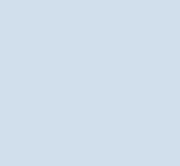
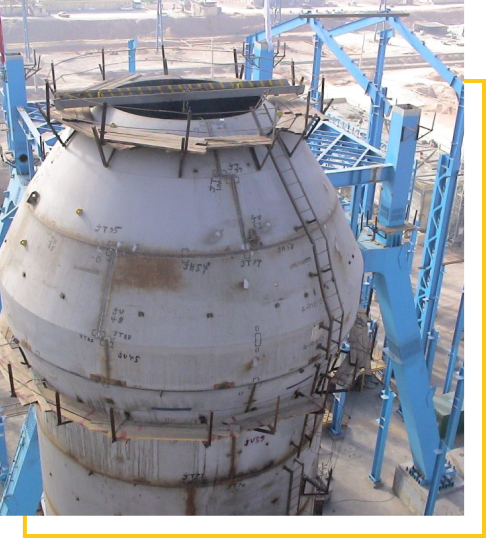
Chemical composition (chemical formula) of sponge iron
cutie | Composition |
---|---|
86-85.9% | Fe (total) |
Min 90% | Fe (metallization) |
78.5-82% | Fe (metal) |
1.3-2% | C |
Max 0.01% | S |
Max 0.1% | P |
Max 5.5% | SiO2 |
Max 1% | Al2O3 |
Stay in touch with us!
![Div [client_wrapper] (4)](https://tfaaco.com/wp-content/uploads/2024/09/Div-client_wrapper-4.png)
![Div [client_wrapper] (3)](https://tfaaco.com/wp-content/uploads/2024/09/Div-client_wrapper-3.png)
![Div [client_wrapper] (2)](https://tfaaco.com/wp-content/uploads/2024/09/Div-client_wrapper-2.png)
![Div [client_wrapper] (1)](https://tfaaco.com/wp-content/uploads/2024/09/Div-client_wrapper-1.png)
![Div [client_wrapper]](https://tfaaco.com/wp-content/uploads/2024/09/Div-client_wrapper.png)